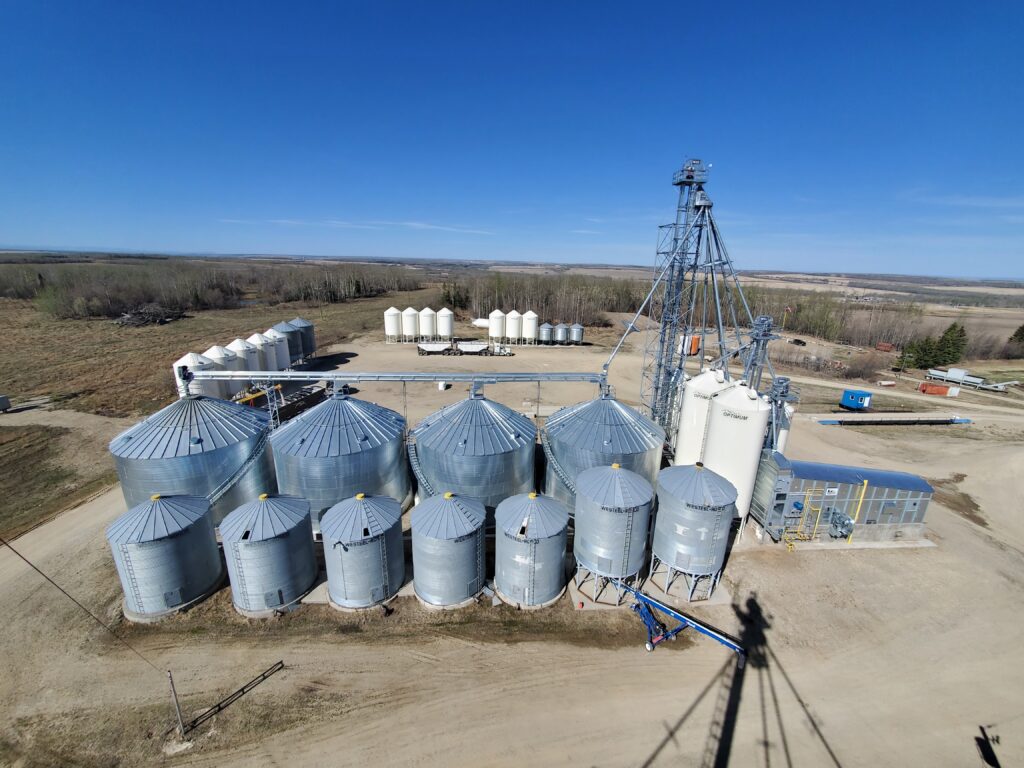
Creating efficiencies on the farm is often a top priority when considering capital and equipment investments. Equipment breakdowns, insufficient storage, or using inadequate tools can lead to time and production losses, ultimately impacting long-term profitability. Peace View Colony in Taylor, BC faced these challenges during their 2020 harvest. They required a more efficient way to handle their crops, including quick unloading, efficient grain drying, and increased on-site storage capacity. To overcome these obstacles, they collaborated with Penner Farm Services Alberta, an industry leader in providing customized solutions for farming operations.
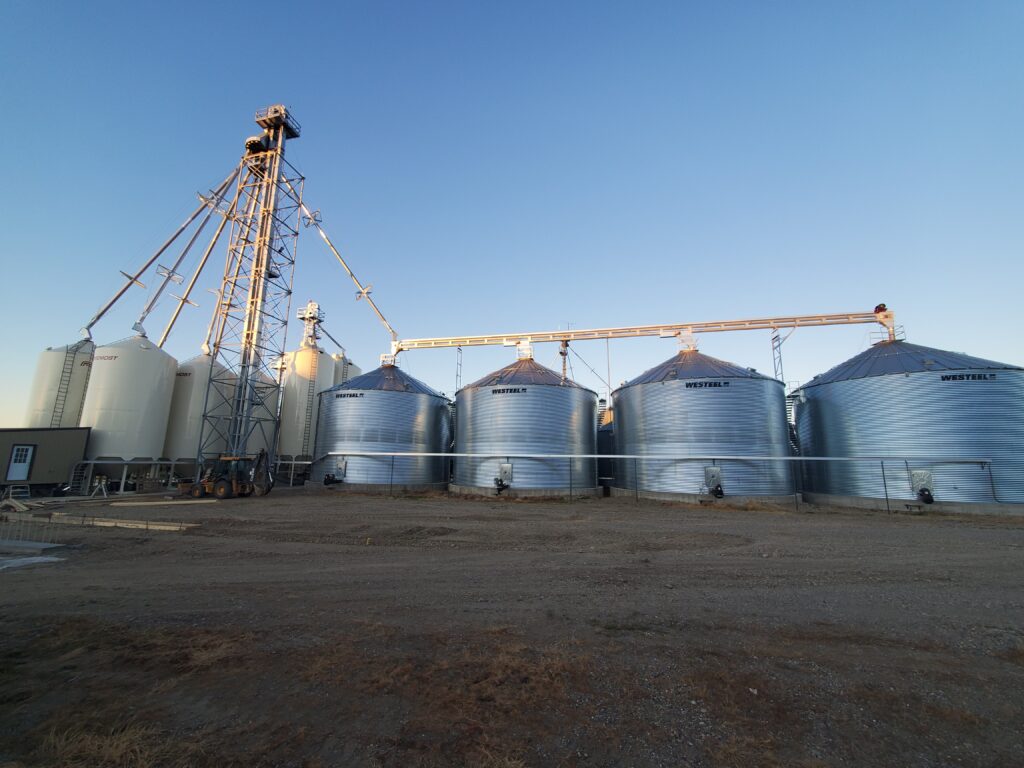
Penner Farm Services Alberta offered the innovative RAD Round Bottom Drags, designed to receive grain from incoming trucks. This efficient receiving drag delivers grain at an average rate of 8,000 bushels per hour (bph) to a 115ft RAD Bucket Elevator. Once in the elevator, an electric distributor allows for grain placement into either Dry Storage or Wet Storage. Wet grain is stored in six 5,000-bushel bins until it is ready for the drying process. The colony has the flexibility to draw grain from multiple bins, blend products while transferring to the dryer, or dry one bin at a time. RAD 10″ Galvanized Augers, powered by VFDs, efficiently transfer wet grain into a RAD Round Bottom Drag Conveyor, which feeds into a RAD 3,500bph Wet Leg for filling the grain dryer or re-entering the main system.
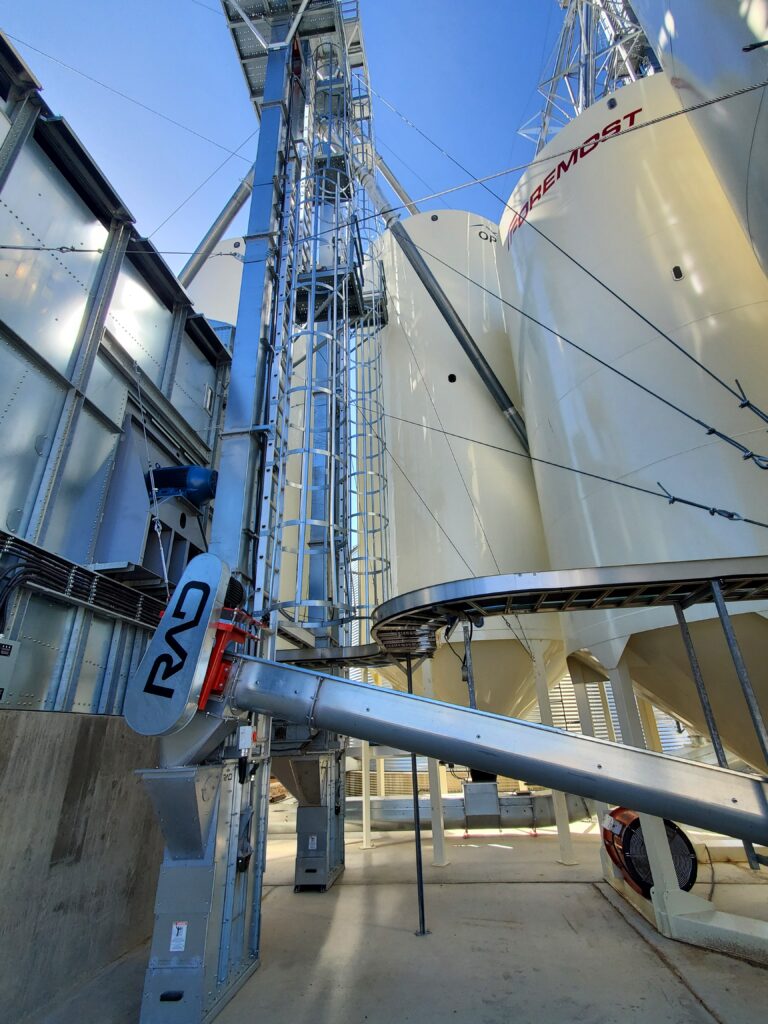
After the drying process, a RAD elevator transfers the dry grain into two Optimum Manufacturing “cooling bins.” These bins, equipped with Rocket Aeration, enable the colony to cool the grain to the desired temperature before transferring it to long-term storage. Subsequently, a RAD 18″ Round Bottom Conveyor transports the grain back to the main elevator at a rate of 8,000bph. The dry grain has the flexibility to either go to long-term storage or be directed to load out bins. To facilitate movement into multiple bins at a rate of 8,000bph, a RAD 12″ Double Run tube conveyor was used above the long-term storage bins.
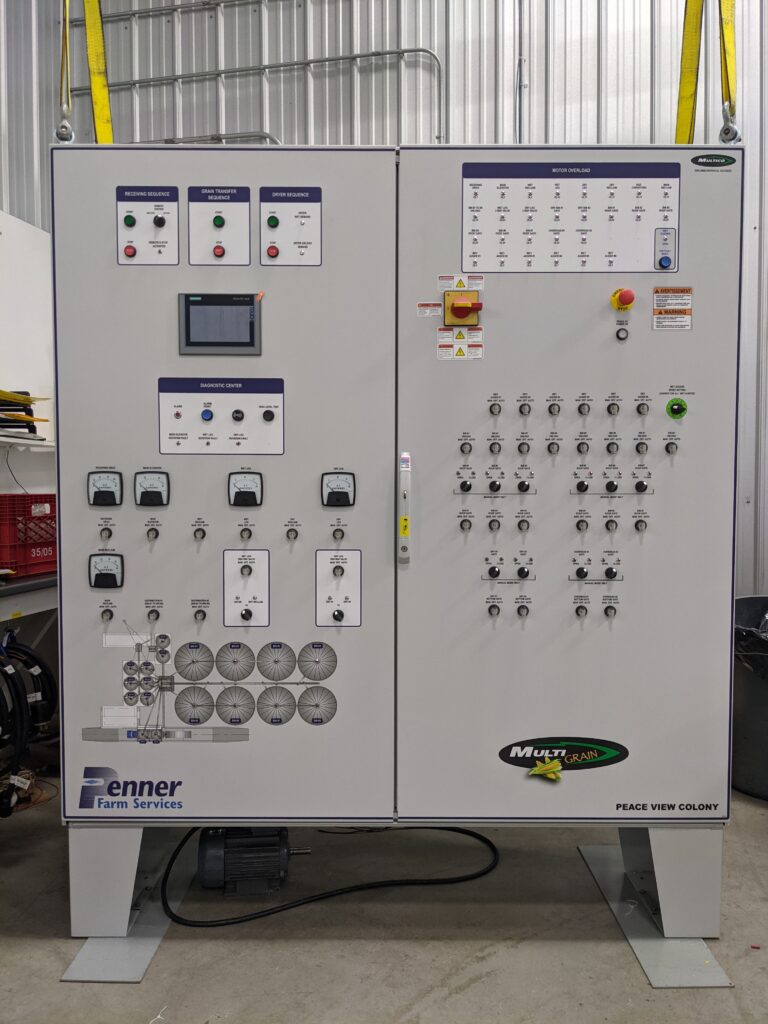
All grain receiving, wet handling, cooling, and transferring processes are conveniently controlled via a Multico Control Panel. This comprehensive control panel allows the colony to operate the entire system from a local control room. By utilizing electric gates, electric distributors, and automatic shutdown/startup sequences, grain transfer is seamlessly executed.
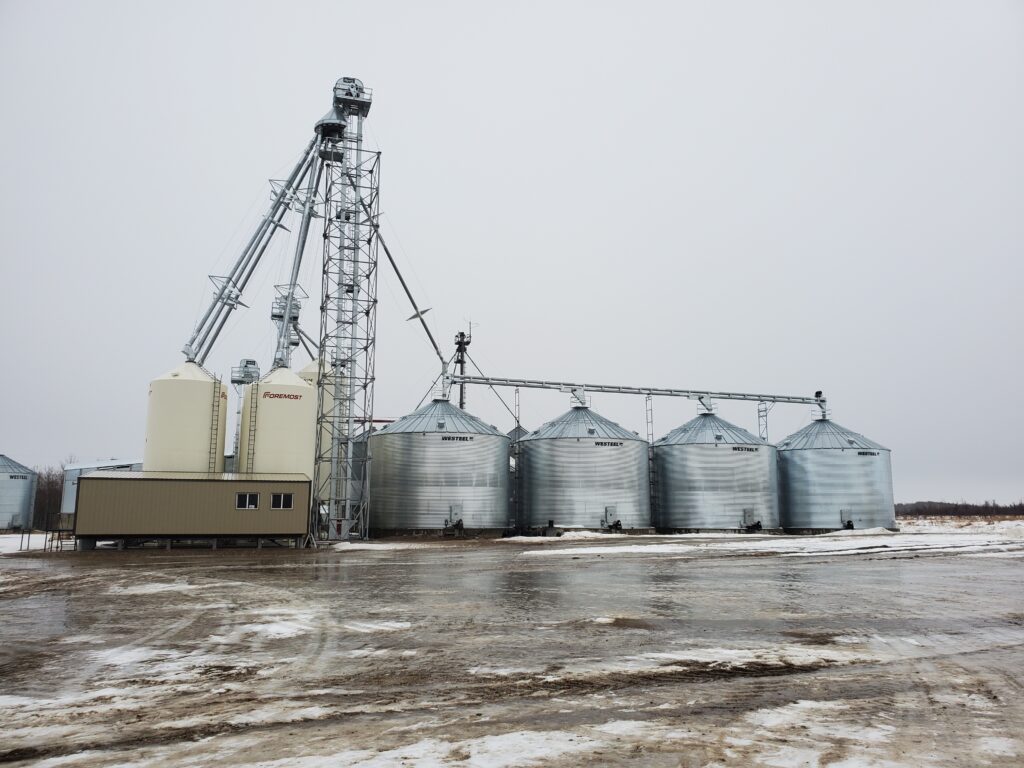
Prior to the installation of this new system, the colony had three flat-bottom bins with a capacity of approximately 105,000 bushels of dry grain. With the newly implemented system, the colony now has the potential to store up to 293,000 bushels of dry grain and 35,000 bushels of wet grain, significantly increasing their storage capacity.
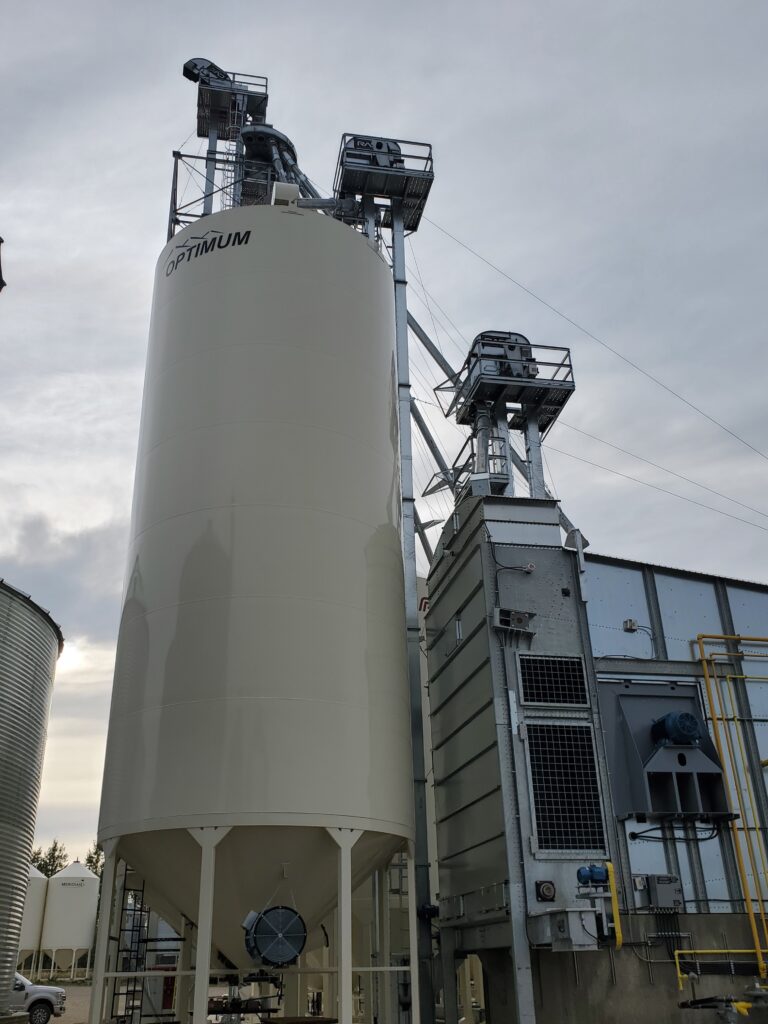
The system has allowed for a more efficient harvest and utilization of the grain on the colony. The other benefit of the system will be its ability to expand with the needs of the colony. Future plans include overhead load out bins and installation of RAD Reclaim conveyers to bring the grain from long term storage back to the main elevator, which will allow them to fill the overhead bins. Every farm is different and at Penner Farm Services we pride ourselves on working closely with our farming partners to customize solutions that will work for them today and grow with them into the future. For more information on this project or any of the systems or solutions above contact Penner Farm Services Alberta Today and speak with one of our Grain Handling Experts.